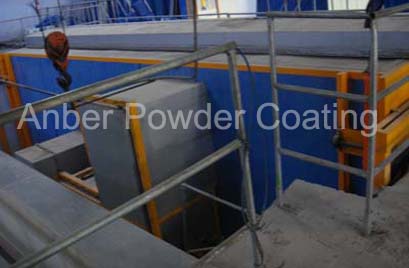
Drying oven with batch design
.jpg)
Top-door-open design for easy access of objects by lifting crane (matching with immersion tank pretreatment system)
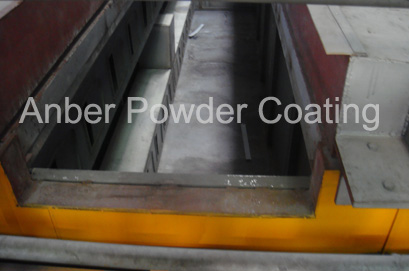
Inner structure of tank-shape drying oven oven
.jpg)
Side air inlet & outlet for a good circulation of heated ait (Tank-shape dryoff oven)
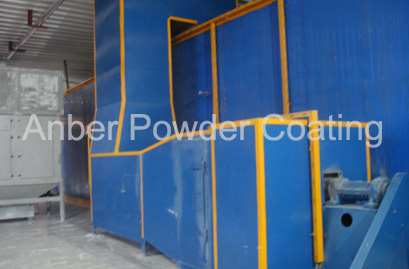
Air pipeline for curing oven
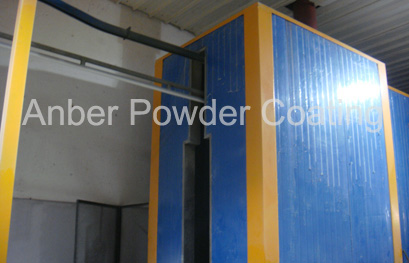
End thermal insulation for tunnel oven
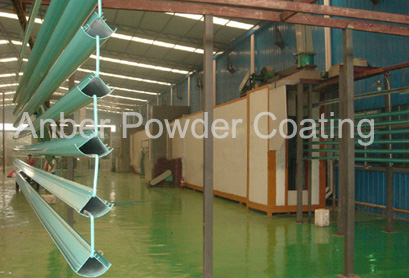
Curing tunnel for aluminium profile powder coating linel
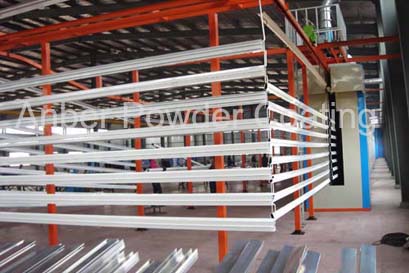
End outlet for powder curing oven
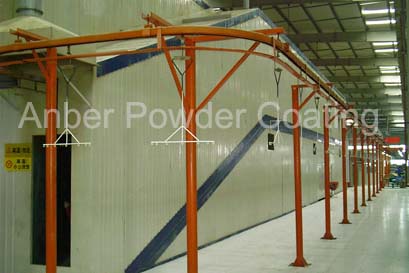
Bridge type curing oven
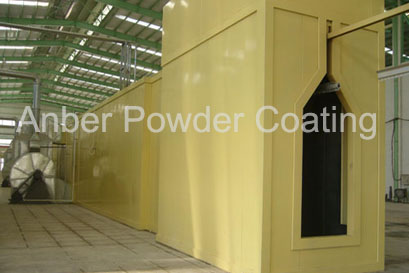
Curing oven for aluminium profile powder painting line
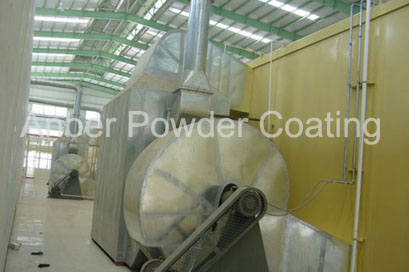
Heated air circulation unit for curing oven
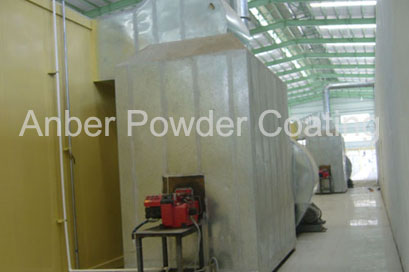
Imported gas burner
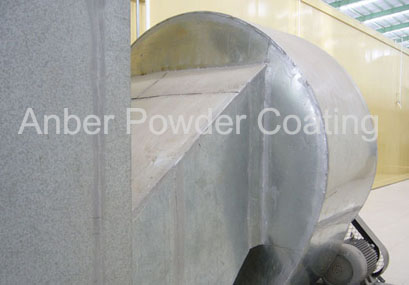
Air pipeline for gas-fired curing furnace
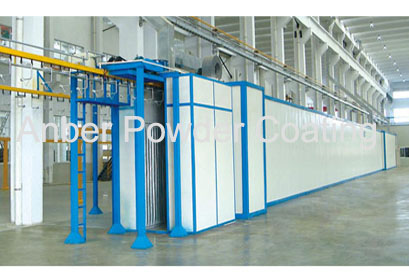
Overall view of curing tunnel
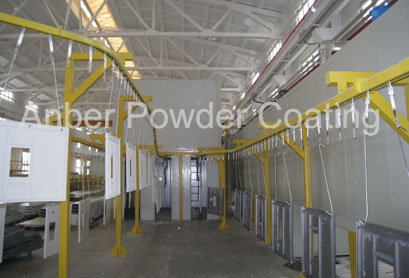
Compact oven tunnel for both drying and curing
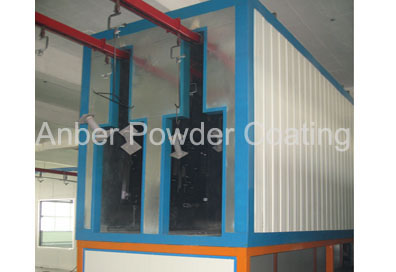
Drying off & curing combined oven

Gas fired curing oven with bottom up vertical hot air convection
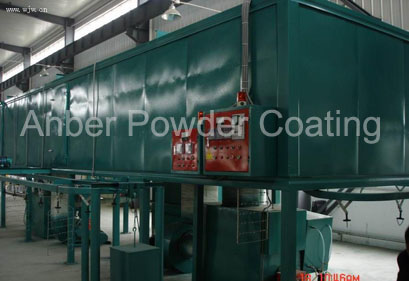
Control cabinet for curing tunnel
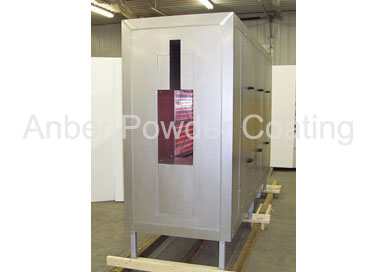
IR curing oven with conveyorized system
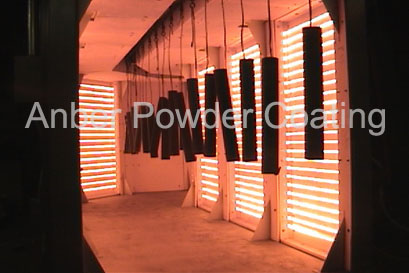
Infrared tunnel oven
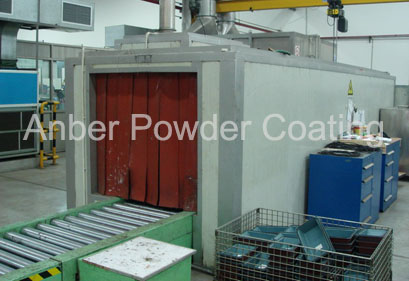
Heating oven with roller conveyor
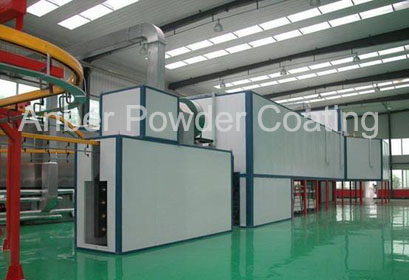
Tunnel-shape curing oven for high automation
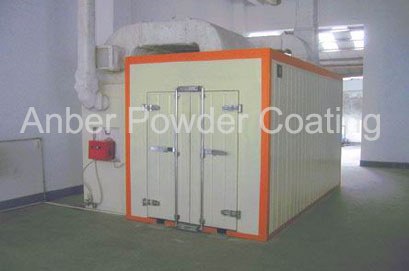
Bath oven for small investment
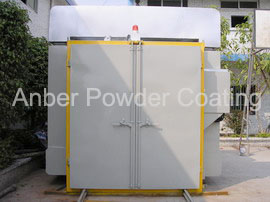
Gas-fired batch oven
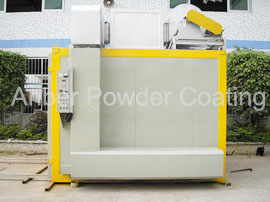
Gas heated batch oven for manual powdercoating line
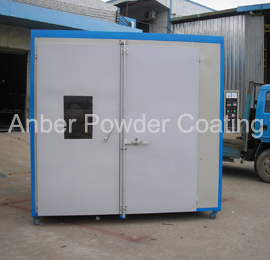
Electrical heating batch oven
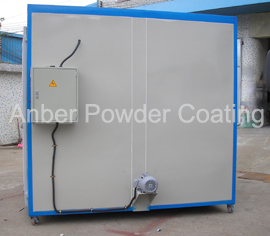
Box type oven with electrical heating
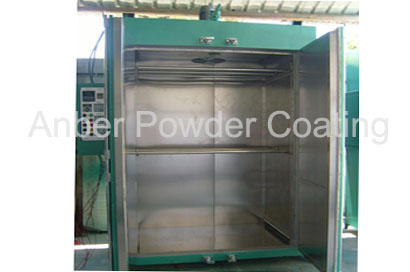
Oven with hanging bar
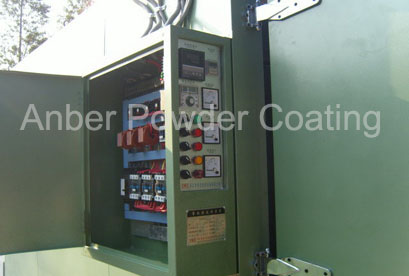
Control cabinet for batch oven
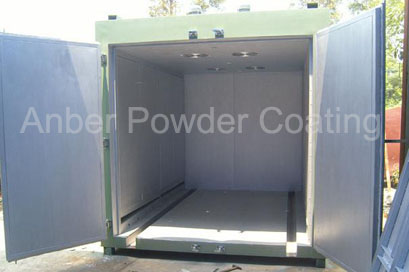
Batch oven with trolley feeding
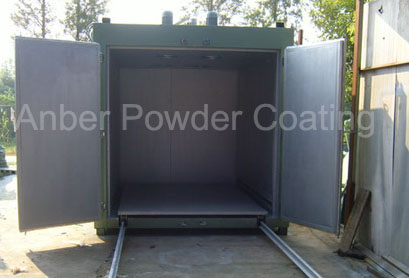
Batch oven with 3m guide track for feeding trolley
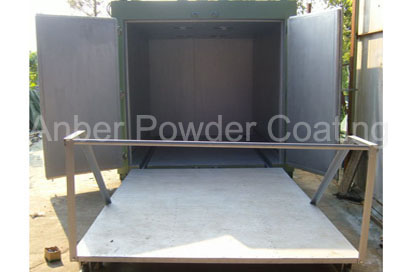
Electrical heated trolley oven
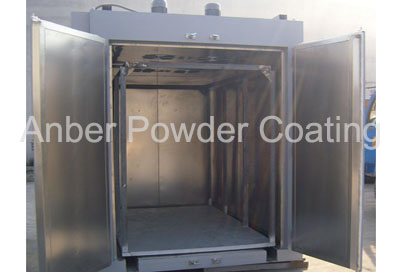
Inner strcture design of batch oven
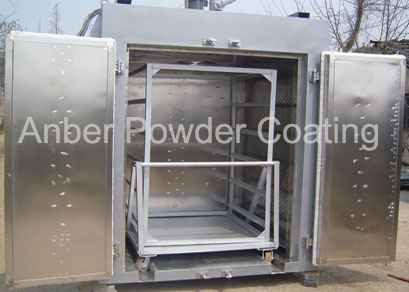
Stainless steel batch oven