|
 |
Sitemap |
 |
FAQ |
Welcome to Anber Powder Coating Co., Ltd's website! |
|
|
Powder coating lines
Components of powder coating line
|
|
For a high demand of efficiency and automation, these economical tanks can be replaced by vertical shower type,please click here for detail.
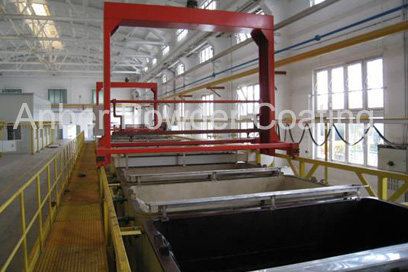 Stainless steel immersion tank with overhead crane
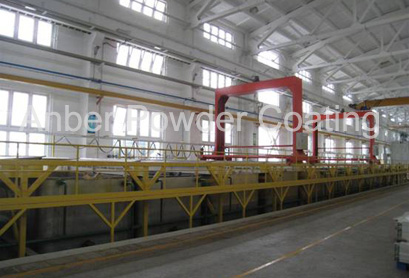 Side view of stainless steel immersion pretreatment system
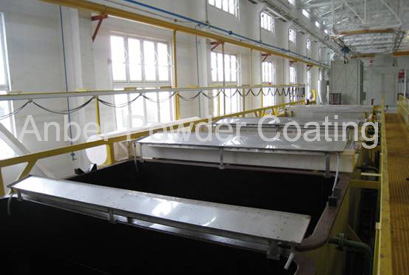 Drain board between 2 tank helps to reduce chemical pollution
.jpg) Lifting crane for easy access of objects into immersion tanks (Horizontal pretreatment system)
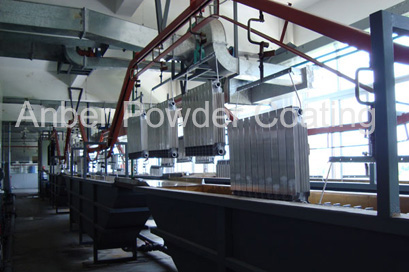 Space-saving chemical cleaning system for rediator
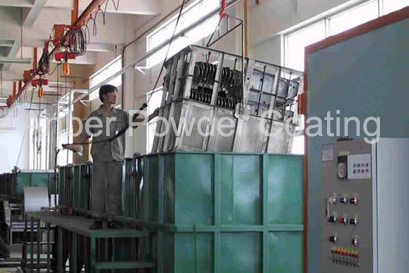 Deep immersion tank for large objects
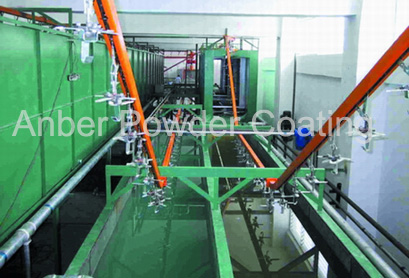 In-line dip washer with conveyorized system
.jpg) Economical concrete tanks for large control banibet (Immersion washer)
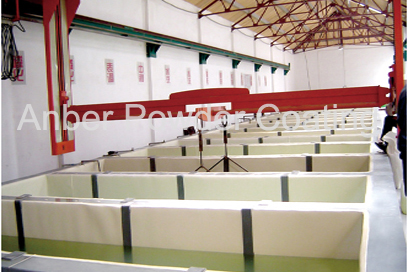 Cement solution tanks with PVC anti-corrosion linings
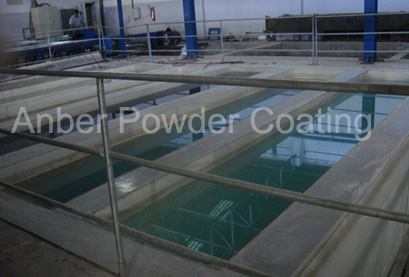 Cement solution tanks for chemical cleaning
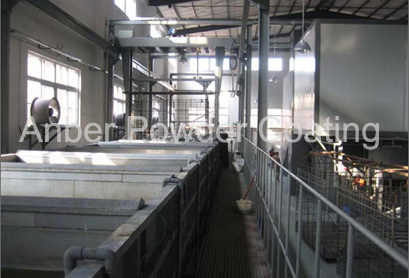 Off-line dip washer system for the preparation of powder coating line
Pretreatment system: preparation for powder adhesion
Proper surface preparation is the single most important aspect of a powder finishing system should you wish to maximise powder performance. The procedure required to obtain a suitably prepared surface depend heavily on the type of substrate but in most cases the following steps are required:
● Cleaning
The cleaner will depend on both the substrate and the soils to be removed e.g. synthetic draw lubricants are much easier to remove than a buffing or polishing compound. Metal oxides (rust) need to be removed at this point as they will act as a barrier to powder coating film adhesion. This is normally achieved by using an acid deruster
● Conversion coating
Conversion coatings are materials and processes that impart corrosion resistance better adhesion properties to a metal substrate. The type of conversion coating depends heavily on the nature of the substrate as well as the desired properties of the coating.
Aluminium - The aluminium surface is treated with a chromate conversion coating to produce a surface layer that comprises of both aluminium and chrome oxides. This is a smooth uniform surface that is chemically inert and allows good adhesion of the organic coating.
Iron & Steel - Zinc Phosphate or Iron Phosphate is used depending on the mechanical properties and corrosion resistance required from the finished part.
● Passivation
A passivator (seal rinse) is applied over a zinc or iron phosphate to increase the corrosion resistance of the coating and to improve adhesion of paint and organic finishes. Passivation is important if components are going to be stored or transported between chemical treatment and powder coating.
● Rinsing
The work pieces are rinsed between stages to prevent cross contamination of process solutions and to reduce chemical consumption. The final rinse prior to drying is to remove any unreacted chemical or salts that could adversely affect adhesion.
Features of immersion tank pretreatment system
● Advantages of immersion tank pretreatment system
1.Low cost installation
2.Off line design for space saving
3.Better protection in difficult areas
4.Small components easily batched
5.Simple to maintain
6.Flexible chemistries can be used
● Disadvantages of immersion tank pretreatment system
1.Not easy to automate
2.Tends to give dusty coating
3.Large tanks require long heat up time
4.Use more energy
5.Quality can vary as manual operation is used
Typical Pretreatment Example: only for your reference
● For aluminium objects
1.Pickling: 3-5 mins (Room temp.)
2.1st Rinsing: 1-2 mins (Room temp.)
3.2nd Rinsing: 1-2 mins (Room temp.)
4.Chromizing: 2-5 mins (25-35℃)
5.3rd Rinsing: 1-2 mins (Room temp.)
6.Final rinsing: 1-2 mins (Room temp.)
● For steel & iron objects
1.Degreasing: 2 mins (50-65℃)
2.1st Rinsing: 1 min (Room temp.)
3.2nd Rinsing: 1 min (Room temp.)
4.Surface conditioning: 1 min (Room temp.)
5.Phosphating: 2.5 mins (35-45℃)
6.Final DI Rinsing: 0.5 min (Room temp.)
Note: The above pretreatment examples are only for reference. We advise consulting your chemical supplier to obtain the correct conditions to meet the required specifications. We stress that all chemical pretreatment processes must be maintained to the chemical suppliers specification to ensure continuous quality powder coating.

|
|
|